
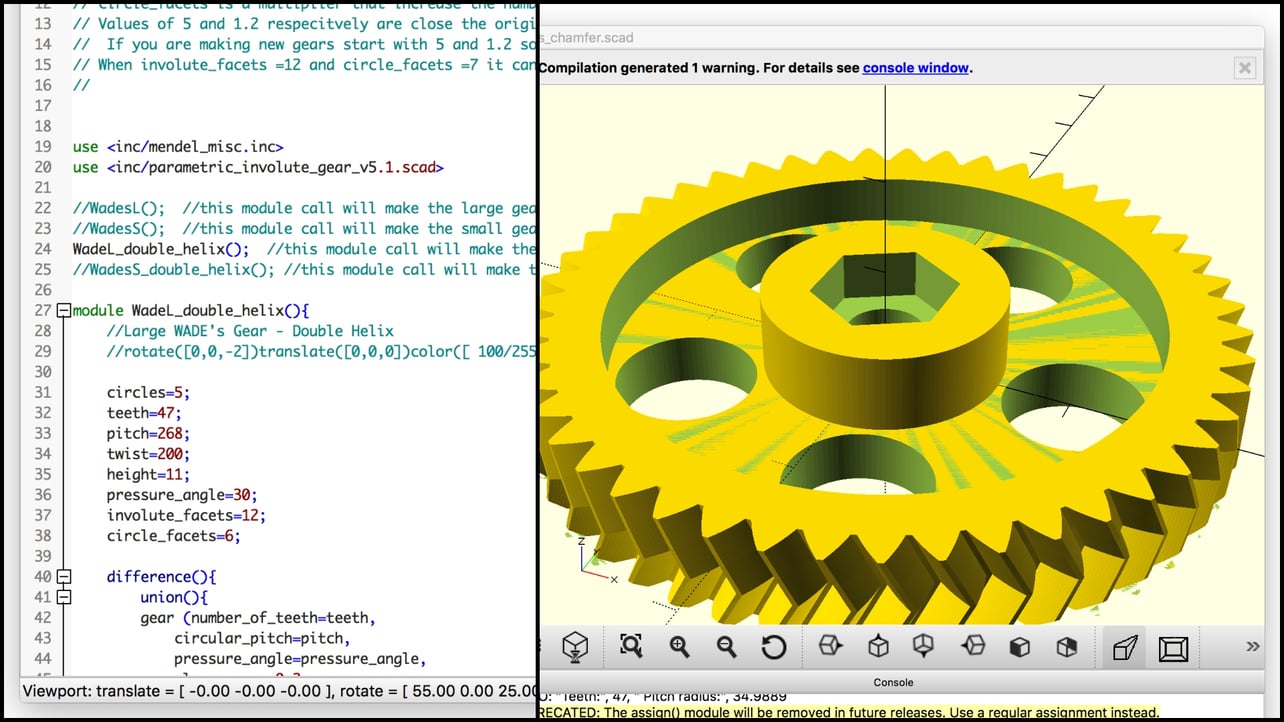
A program in Java is developed to recognize geometric entities, with their directrix contained in a solid model. What is the difference between a parametric learning algorithm and a nonparametric learning algorithm The term non-parametric might sound a bit confusing at first: non-parametric does not mean that they have NO parameters On the contrary, non-parametric models (can) become more and more complex with an increasing amount of data. And form finding using parametric 3D modelling and simulation tools. By using better form finding algorithms, resulting in highly advanced software.Automatic recognition of geometric and topological features from solid models has a great impact on the various levels of integration.
Parametric 3D Modeling Algorithms Series Featuring Scholars
The approach is very different from 2D CAD or traditional 3D modeling.LA’s Disney Concert Hall. Pathways to Just Digital Future Watch this tech inequality series featuring scholars, practitioners, & activistsThe rules of a parametric design are often based on algorithms, in which case we. Computer-numeric controlled (CNC) milling machines were first developed in the early 1950s, primarily for military and aviation uses the first CNC patent was awarded to MIT in 1952. In this section our focus is on parametric 3D objects, and specifically on parametric 3D objects that can (or could) be realized through computer-aided fabrication and direct-digital manufacture. The algorithm works efficiently for complex models built using volumetric decomposition as well as hybrid of hint based and volumetric decomposition approaches. This paper presents geometric algorithms to recognize features from various 3D CAD models of prismatic parts.
The same program that was used to design the Mirage fighter jet was now being used to design a fish sculpture.CATIA fundamentally redefined architectural digital modeling. So, a Gehry employee turned to CATIA, a C++ software package developed by an aerospace manufacturer. Gehry’s Barcelona Fish While designing a 50 meter undulating fish sculpture for Barcelona’s 1992 Olympics, Gehry realized that the available 2D programs were unable to model the sculpture’s curvature. His team was then challenged to construct these fantastical shapes in a structurally sound and cost-effective manner, necessitating extremely precise models. By the 1980’s, he had defined a new architectural style characterized by playful geometric complexity and was infamous for creating his forms through freehanded sketches followed by “tearing scraps of paper, gluing and taping them together, crinkling cardboard, and adding apples and Perrier bottles” to create crude physical models.
As a result, GT advised on several projects (like the 2008 Bird’s Nest Stadium) which that provided insight into how other design firms operated.Several future opportunities exist for this service: GT could potentially expand its consulting operations to applications necessitating accurate measurements and efficient space utilization, such as dam designs or electric grids.Collaboration: GT developed GTeam, a project-based collaboration platform enabling players in the design process to share and consolidate data. Digital Project Model for the Beijing Olympics stadium designed by Herzog + de Meuron Project Delivery Service: GT provided consulting services to other firms, transforming designs into structurally-sound buildings (and saving ~10% of the building’s cost ). Supplementing his architectural firm with a technology/software firm fundamentally changed Gehry’s value proposition to clients: working together, the companies were now responsible for the entire digital model (materials, specifications, and costs), removing this step from the contractor’s role and “bring fabrication expertise forward into design.” GT continued to innovate through a number of avenues, including:Customization: GT addressed an untapped market potential by creating Digital Project, a CATIA-based software designed specifically for architecture firms that provided design support for construction scheduling and plumbing. However, with CATIA, contractors were able to (i) become involved earlier in the design process and (ii) refer directly to Gehry’s 3D digital models, saving time, money, and making the entire design chain more efficient.To capitalize on this innovation, Gehry Technologies (GT) was founded in 2002 to facilitate visionary designs while keeping cost and schedule in line for clients. Utilizing this software, the Barcelona Fish was built in six months within budget.A 3D Bézier surface with control points CATIA version 3, in 1988 Previously, architecture firms (with minimal collaboration) delivered 2D drawings to a contractor, who then then created its own set of drawings/models that had to be approved by the architect before moving to fabrication.
Screenshot of GTeam GT could potentially go a step further by integrating raw material sourcing into the GTeam platform to optimize design specifications and costs, and by expanding the GTeam collaboration platform to other industries necessitating the sharing of information in a track-able fashion, such as law firms, educational institutions, or electronics manufacturers. Increased collaboration led to the completion of groundbreaking projects on time, under budget, and with fewer change orders. GT also addressed a major industry concern: “given the financial and legal structures that conventionally discourage architects, engineers, and contractors from sharing information so freely, the software also logs each move for legal record-keeping.” As a result, subcontractors and fabricators were able to work with architects and contractors during the design phase, which reduced errors, minimized redundant communication, and enabled the design team to incorporate feedback from various trade experts and specialists.

